DESIGNING THE NAVAL
by Andrea Bison, Massimo Cadorin, Alberto Cavallini
Until then, in the artificial indoor climate sector Manens-Tifs (and previously, the four companies that, by integrating, generated it) had operated only in the context of the land-based civil built environment (residential, commercial, public and private tertiary), with limited excursions to the industrial sector. In 2013, Fincantieri, a world leader in the construction of cruise ships, proposed to Manens-Tifs to take charge of the design of the HVAC systems of the ships to be built in the future, with the aim of changing the well-established approach of entrusting the design of the plant systems to the same parties then responsible for supplying the machines and/or performing the shipboard assemblies (in other words, the classic “turnkey” procedure).
The objective of this change in operational strategy (in some respects epochal) was twofold: on the one hand, being able to make use of a “third-party” design would guarantee, in the context of commercial negotiations during the purchase phase, greater bargaining power; on the other hand, to introduce even in this sector energy-saving and environmentally friendly solutions that, then already widely applied in land-based plant engineering, were still completely foreign to the naval sector, which was reluctant to abandon safe and established traditional technologies in favour of innovation.
The opportunity was jumped at, with the enthusiasm of being able to explore new horizons, but also with the awareness of the substantial difference in approach between land-based construction and naval design: to this end the Ship Business Unit was then created.
Not only considering ancillary activities, there are many distinctions in design related to environmental comfort in civil buildings and ship cruising, not all of them minor or trivial. The specificities differ right from the stage of acquisition of the assignment where, in naval, this is direct from the Client, without competition, with cross-examination on the quantification and single stage in the execution. In addition, the designer is accountable only for the project, coordination is the responsibility of the Client, and construction aspects are the responsibility of the qualified shipyards.
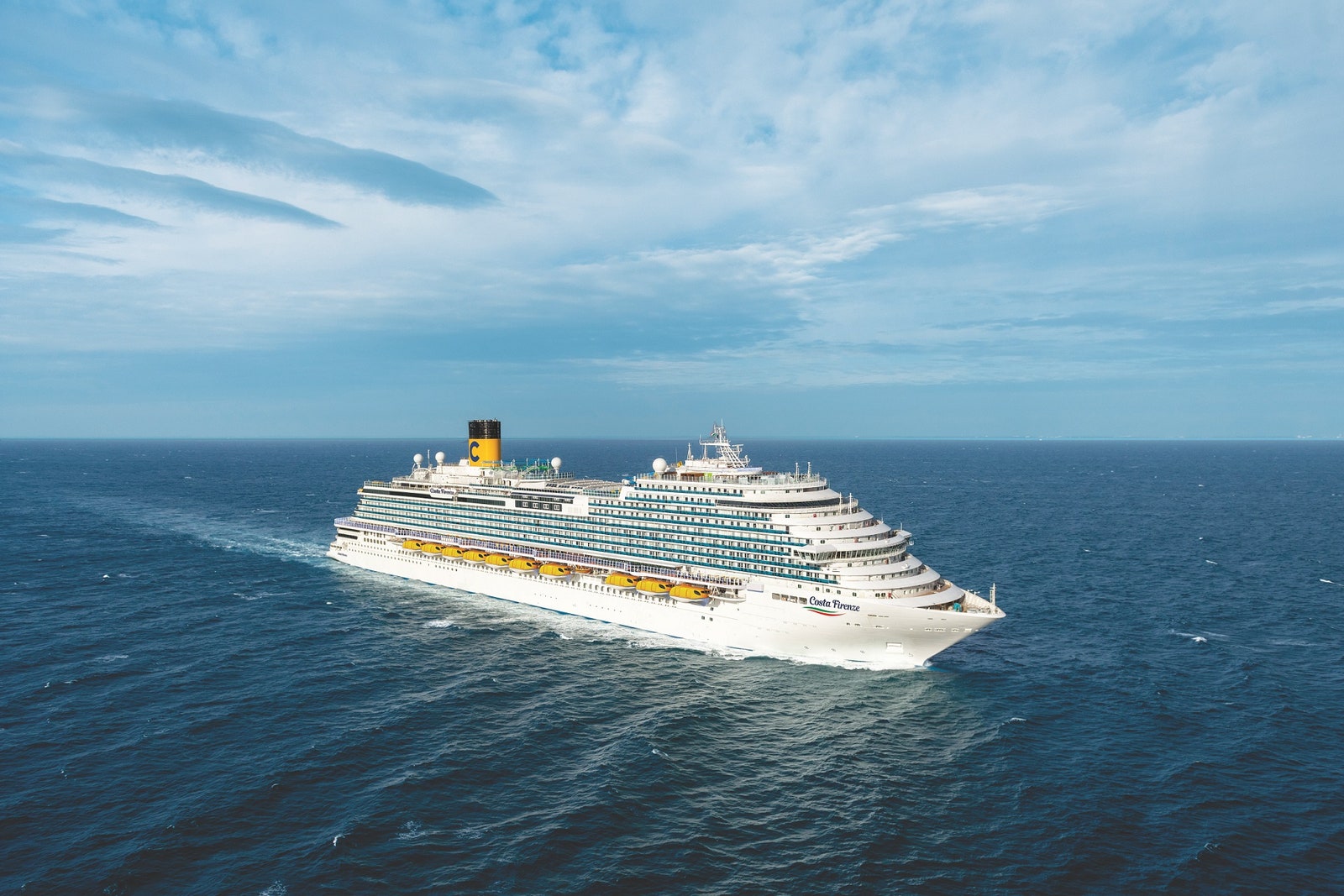
COSTA FIRENZE, by Costa Crociere: 135 000 t s.l., can accomodate up to 5260 passengers with 1480 crew members
As for the scheduling of the different design phases, continuous deliveries are required in the naval sector, harmonized with the progress of the work, with a production system akin to the island work of an assembly line; the need for variations and modifications is codified for the entire life of the project. Design in the naval field thus requires continuous and widespread interaction with the Client, with meetings not only limited to specific needs.
About external design climatic conditions, compared to the terrestrial context far more extreme must be the reference values in naval design for both summer and winter situations, in relation to all the possible routes to which the vessel may be destined; it must also be considered that the situation may widely vary at short times during the same voyage. On the other hand, it is always necessary to ensure, in the passenger areas, internal microclimatic conditions of a luxury hotel, giving possibility, in the cabins, of wide choice on the part of the passenger.
A critical situation is also found in the need for compliance with technical regulations, which are often hybrid, since in this area it is required to submit to the set of international standards for naval aspects, according to the interpretations of the classification body in charge, and in addition to specific national standards depending on the flag, along with all others in relation to the need for access to definite territorial waters and ports.
The limited availability of space for the placement of equipment and the construction of plant passages is perhaps the most critical element that the designer must deal with, an obvious consequence of the great economic value of the surface area available to passengers: the sacrifice of a balcony cabin results in a loss of value of the ship of more than 200 000 €. Adding to the shortage of space allowed is its unfortunate location, confined mainly to the level of the lower hold, again so as not to occupy commercially valuable areas. There are also major restrictions on the construction of air intakes or drains in the outer bulwarks, dictated both by regulations on the risk of flooding, and in order not to take away sea-view surface area from more appropriate use and to avoid inconvenience in the outer areas for passenger use. The drains are to be concentrated in the funnels area, to safeguard comfort in the remaining open spaces and to prevent spill over into public areas, a risk accentuated by the motion of the ship itself (typically 18÷24 kn, or 33÷44 km/h). This is compounded by drastic size limits imposed on equipment and distribution infrastructure. It should be considered that naval plant engineering always requires very stringent redundancies, due to the difficulties of off-site intervention and the technical time required to obtain spare parts. This situation, already inherently complicated to solve from the distribution point of view, aggravates many other design issues. To cite one among them is the imperative need to ensure the containment of plant-born noise transmission to cruise ship areas.
With reference to two of the most current design goals in the buildings’ construction field, namely energy conservation and environmental sustainability, the attitude in ship design is somewhat peculiar.
Regarding the first point, there is little interest in sensible heat recovery from the exhaust air, given the abundance of the waste heat available from electrical generation and propulsion; convenient instead is latent recovery, due to possible critical operating situations, such as in Caribbean routes. The need for large oversizing is likely to result in less attention to optimization and efficiency issues. One must also be aware of the impossibility of subsequent corrective and refinement work since, when operative, the facility is largely inaccessible: the rooms are continuously occupied, with no redundancy of space (an area under maintenance would be completely taken away from cruise passengers and the ship routinely operates with higher occupancy than the base one).
About limiting environmental impact, a difficult balance must be sought with the requirements for simplicity and robustness of the facility, all compounded by the imposed size limits. It cannot be forgotten that, in the operational phase, extreme interventions may require the cutting and subsequent restoration of the structures, exclusively in steel, with the need to secure them against the inevitable high-temperature processing (oxyfuel cutting, welding, grinding); furthermore, the replacement of large machinery after launching is not possible, unless extensive disassembly and installation of temporary handling systems are provided.
A further factor that may delay the entry into this sector of the innovative technologies now in common use in the field of buildings’ HVAC systems lies in the fact that the market makes available only a limited subset of components certified for marine use, with unified standards set by the client; on the part of the designer there is no choice outside the available closed lists. The manufacturers themselves – few and established in a market with attractive margins, but marginal volumes – aware of the difficulties in introducing new products and of the limited competition, tend to consolidate their respective market positions rather than expand their offerings.
Ultimately, in the naval HVAC field, innovation can only make its way gradually; for each new solution, full reliability must be demonstrated under the peculiar operating conditions. Added to this is the need for ship owning companies to be able to have homogeneous fleets, including HVAC components and working fluids (such as refrigerants), to facilitate both crew rotation and the training of maintainers, as well as to reduce the stock of spare parts in warehouses on different continents, which must be able to supply any critical ship element in a very short time.
The Manens-Tifs Ship Unit currently has 20 employees, who on average develop 30 000-35 000 engineering hours annually; in its nine years of operation until June 2022, has intervened on a total of twenty-nine different ships (for five of these also with double assignments), involving some fifteen of the world’s major cruise brands (MSC, HAL, Regent, Seabourn, Virgin, SilverSea, Costa, Carnival, NCL, Ponant, Cunard, Viking, Aida, Princess, MSC-Explora). As of the current date, eight orders are active.
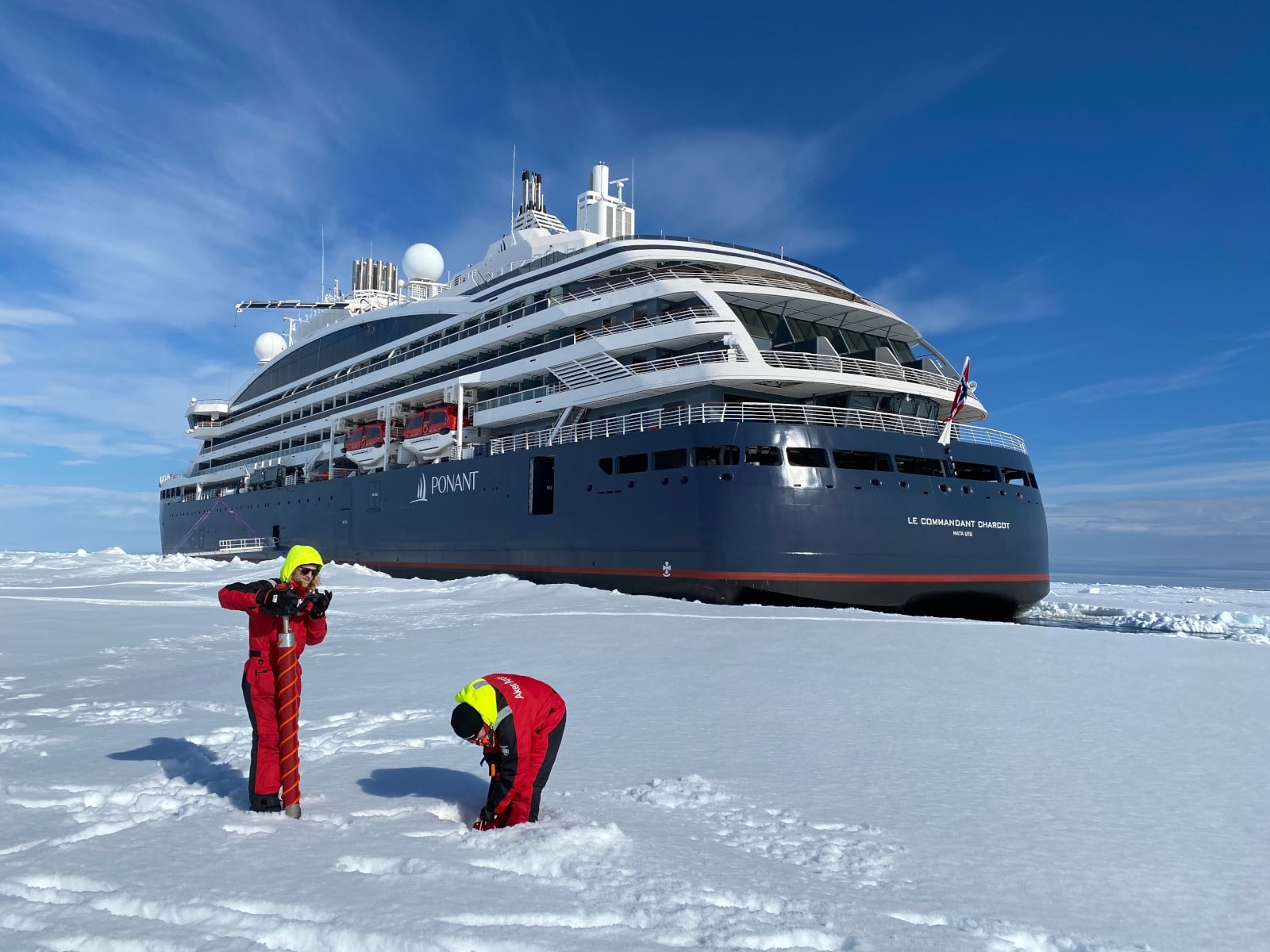
LE COMMANDANT CHARCOT, by Ponant: icebreaker for luxury cruises in glacial seas. It can reach the geographic North Pole.
The characteristics of the ships handled so far by the Ship-Unit lie between the following extremes:
The smallest ship is Le Commandant Charcot (brand Ponant), with a gross tonnage of 31 200 t, length 150 m and maximum width 28 m. It is in the extra-luxury market segment, for 270 passengers and 457 crew members. The design type is of prototype, of Icebreaker, Polar Class 2 and Zero Emission Mode characteristics (with battery electric storage of 5 MWh); the total installed cooling capacity is 3.4 MW with 20 AHUs in place (redundant excluded), with total outside air flow rate of 232 000 m3/h, while the total flow rate of chilled water circuits amounts to 506 m3/h. It required, by M-Tifs Ship Unit, about 6500 h of engineering development. Built at Vard shipyards (in Norway and Romania), it is operational from July 2021.
The largest ship, a true giant of the sea and to date the largest class ever built in our country, is the Sphere (project name, Princess Cruise brand), 175 000 gross tonnage, 345 m long and 42.5 m maximum width. It is in the conventional market segment, for 5560 passengers and 1674 crew members. The design type is prototype, of Dual Fuel characteristics; the total installed refrigeration capacity is 32.8 MW for general services and 3.6 MW serving the electrical rooms, with 92 AHUs in place (redundant excluded), with total outside air flow rate of 1 246 000 m3/h, while the total flow rate of chilled water circuits amounts to 3502 m3/h (including catering uses). It will have required at the end of the project by M-Tifs Ship Unit, about 37 000 h of engineering development. Built by Fincantieri at Monfalcone (Italy), it will be operational from December 2023.
The results indicate that Manens-Tifs’ choice to take on this challenge by bringing a modern and innovative conception of engineering to the naval HVAC sector has been successful, and when, as in this and other cases, a vast and in-depth technical knowledge needs to be combined with a great deal of creativity, vision and imagination, it is no longer possible to speak only of craft, but it is also necessary to invoke the word art, the art of designing.
“To accomplish great things, we must not only act but also dream; not only design but also believe.” (Anatole France, 1844 – 1924).
Andrea Bison (Naval Construction Technical Office Manager)
Massimo Cadorin (TiFS Division Director)
Alberto Cavallini (Advisory Board)